Technical Articles
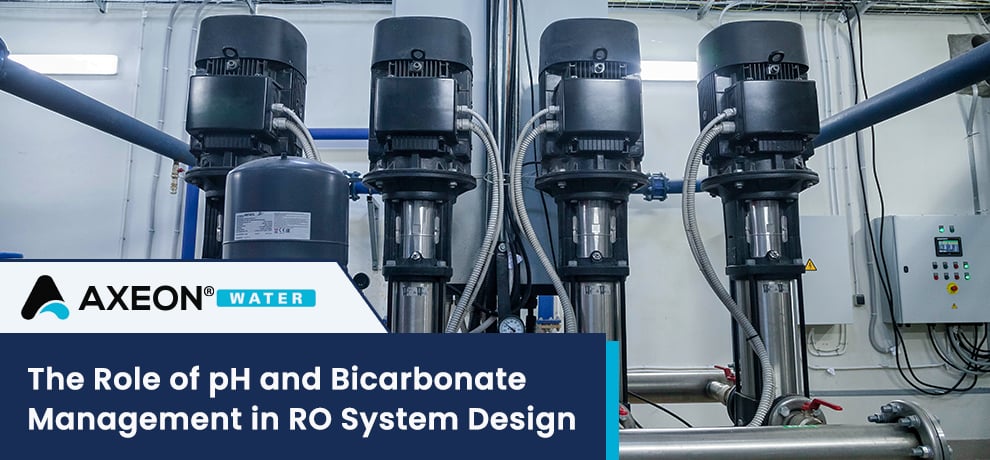
Reverse osmosis (RO) system performance is fundamentally governed by the intricate relationship between pH levels and bicarbonate concentrations in feed water. This chemical equilibrium directly impacts membrane longevity, scaling potential, and overall system efficiency through complex ionic interactions and precipitation dynamics.
AXEON Water Technologies, with over 35 years of membrane filtration expertise, has pioneered advanced pH control solutions that optimize RO system performance while protecting valuable membrane assets. Our comprehensive approach integrates sophisticated monitoring systems with precise chemical dosing to maintain optimal operating conditions.
The seven critical aspects of pH-bicarbonate management in RO systems are:- Understanding the pH-alkalinity balance in feed water, which establishes the foundation for proper system operation
- Optimizing membrane performance through precise pH control mechanisms
- Calculating and monitoring bicarbonate scaling potential to prevent membrane fouling
- Designing effective antiscalant dosing systems that prevent precipitation
- Implementing real-time chemical equilibrium monitoring protocols
- Preventing membrane degradation through proactive pH management
- Establishing long-term system protection strategies for sustained performance
These interconnected elements form a comprehensive framework for maintaining peak RO system efficiency. When properly managed, this approach ensures maximum permeate production while minimizing operational issues related to scaling, fouling, and membrane damage.
Through the integration of AXEON's advanced pH neutralization systems and chemical injection technologies, operators can maintain optimal chemical conditions that maximize system longevity and performance. This systematic approach has been proven across thousands of installations, from commercial applications to industrial-scale water treatment facilities.
Understanding pH-Alkalinity Balance in Feed Water
The relationship between pH and alkalinity in reverse osmosis systems represents a critical chemical equilibrium that directly impacts membrane performance and system longevity. This balance is governed by the carbonic acid-bicarbonate buffer system, which follows the equilibrium equation:


Optimal Operating Parameters for RO Systems
Parameter | Acceptable Range | Optimal Range |
---|---|---|
pH | 2-11 | 6.5-7.5 |
Total Alkalinity | 0-400 mg/L | 50-150 mg/L |
Bicarbonate | 0-300 mg/L | 60-180 mg/L |
The buffer capacity (β) of the system can be calculated using:

- Precise dosing control mechanisms
- Real-time pH monitoring
- Automated adjustment systems
- Integrated feed water analysis
This controlled environment ensures:
- Maximum membrane flux rates
- Reduced scaling potential
- Extended membrane life
- Optimal rejection rates
For systems operating outside standard parameters, AXEON's Chemical Injection Systems provide automated pH correction through proportional dosing control, maintaining ideal operating conditions for maximum system efficiency.
Optimize Membrane Performance Through pH Control
Reverse osmosis membrane performance is critically dependent on maintaining optimal pH levels, with operating ranges between pH 2-11 for standard operation and pH 6.5-7.5 for peak performance. This narrow optimal range directly influences membrane flux rates, salt rejection efficiency, and long-term system reliability.
Performance Impact Analysis
The relationship between pH and membrane performance follows a distinct pattern:- Flux rates peak within pH 6.5-7.5, declining by up to 20% outside this range
- Salt rejection efficiency maintains >98.5% stability between pH 5-8
- Membrane longevity decreases significantly at pH extremes
Feed Water Type | Optimal pH Range | Minimum TDS Rejection |
---|---|---|
Municipal Water | 6.8 - 7.2 | 98.5% |
Brackish Water | 6.5 - 7.0 | 99.0% |
Industrial Process | 6.0 - 7.5 | 97.5% |
- Precipitation of metallic hydroxides above pH 8.0
- Calcium carbonate scaling above pH 7.5
- Colloidal destabilization below pH 6.0
AXEON's HF5-Series Ultra Low Energy Membranes incorporate advanced thin-film composite technology that maintains stable performance across broader pH ranges. The proprietary membrane chemistry provides enhanced resistance to pH-induced degradation while delivering superior flux rates.
To mitigate flux decline and optimize rejection rates, AXEON's automated pH control systems provide:- Real-time pH monitoring and adjustment
- Precise chemical dosing control
- Automated feed water correction
- Integrated antiscalant dosing
Proper pH control serves as the foundation for optimal system performance, directly impacting scaling potential and membrane longevity. The next critical consideration is managing bicarbonate scaling potential, which becomes increasingly important as system recovery rates increase.
Calculate Bicarbonate Scaling Potential
Bicarbonate scaling occurs when dissolved calcium and carbonate ions exceed their solubility limits and precipitate as calcium carbonate (CaCO₃) on membrane surfaces. This precipitation potential can be quantified using established scaling indices and equilibrium calculations.
The calcium carbonate precipitation potential depends on the following equilibrium equation:

The Langelier Saturation Index (LSI) predicts scaling tendency through:

Where pHs is the pH at saturation, calculated using total dissolved solids, calcium hardness, alkalinity, and temperature.
Water Type | LSI Range | Scaling Potential |
---|---|---|
Soft Water | -2.0 to -0.5 | Non-scaling |
Balanced | -0.5 to +0.5 | Slight scaling |
Hard Water | +0.5 to +2.0 | Heavy scaling |
Temperature significantly impacts bicarbonate equilibrium constants and scaling potential. For every 10°C increase, the calcium carbonate solubility decreases by approximately 15%, accelerating precipitation rates.
AXEON's XP-Series Chemical Injection Systems provide precise antiscalant dosing to prevent scaling:- Electronic timer module with 20:1 turndown control
- Output capacity from 4-30 GPD
- Compatible with most scale inhibitors
The scaling potential can be further managed through AXEON's pH Neutralization Systems, which maintain optimal pH levels between 6.5-7.5 to minimize precipitation risk.
For effective scale prevention:- Calculate system recovery and concentration factor
- Determine scaling indices
- Select appropriate antiscalant dosing
- Monitor membrane performance
This comprehensive approach to scaling management ensures optimal system performance while protecting membrane integrity. Proper antiscalant selection and dosing are critical for maintaining system efficiency and preventing premature membrane replacement.
Design Antiscalant Dosing Systems
Effective antiscalant dosing requires precise chemical injection optimization to prevent membrane scaling while maintaining optimal system performance. The dosing rate calculation follows the fundamental equation:

Chemical Injection Parameters
Feed Water TDS (mg/L) | Dosing Rate (ppm) | Injection Frequency |
---|---|---|
0-1,000 | 2-4 | Continuous |
1,000-2,000 | 4-6 | Continuous |
2,000-5,000 | 6-8 | Continuous |
- Electronic timer-based control module
- Adjustable stroke length (20:1 turndown)
- Flow rates from 0.25 to 30 GPD
- Pressure capabilities up to 150 PSI
The antiscalant dosing control system requires strategic placement of injection points:
- Primary injection: Pre-membrane feed
- Secondary injection: Between stages (if applicable)
- Emergency injection: Post-pH adjustment
System monitoring specifications include:
- Real-time flow measurement
- Pressure differential monitoring
- Chemical tank level sensors
- Automated dose adjustment
- Performance trend analysis
Integration with AXEON's pH Neutralization Systems ensures optimal chemical compatibility through:
- Automated pH monitoring
- Feed-forward control algorithms
- Chemical concentration verification
- Continuous system optimization
Regular calibration and maintenance procedures maintain dosing accuracy:
- Weekly chemical strength verification
- Monthly pump performance checks
- Quarterly system optimization
- Bi-annual comprehensive service
This integrated approach to antiscalant dosing provides comprehensive scaling prevention while optimizing chemical usage and system performance. Proper monitoring and control of these parameters ensures consistent membrane protection and extended system life.
Monitor Chemical Equilibrium Parameters
Effective RO system performance requires comprehensive real-time parameter monitoring to maintain optimal chemical equilibrium conditions. AXEON's S-150/S-200 Controllers provide integrated automation for precise monitoring and control of critical operational parameters.
Critical Monitoring Parameters
Parameter | Operating Range | Monitoring Frequency |
---|---|---|
pH | 6.5-7.5 | Continuous |
TDS | 0-2,000 ppm | Real-time |
Conductivity | 0-5,000 μS/cm | Continuous |
Temperature | 40-85°F | Real-time |
Pressure | 45-200 psi | Continuous |
Flow Rate | System-specific | Real-time |
- Digital pH probes with temperature compensation
- Four-electrode conductivity sensors
- High-precision pressure transducers
- Magnetic flow meters with digital output
AXEON's chemical equilibrium control system utilizes advanced algorithms to maintain optimal operating conditions through:
- Proportional feed control
- Dynamic pH adjustment
- Automated antiscalant dosing
- Temperature-compensated measurements
Calibration protocols require:
- Weekly pH sensor verification
- Monthly conductivity cell cleaning
- Quarterly flow meter validation
- Bi-annual pressure sensor calibration
The S-200 Controller provides enhanced monitoring capabilities:
- Multi-parameter trend analysis
- Automated alarm generation
- Remote monitoring interface
- Data export functionality
This comprehensive monitoring approach ensures early detection of potential scaling or fouling conditions while optimizing chemical usage. The system's predictive maintenance algorithms help prevent membrane degradation through proactive intervention based on real-time parameter monitoring.
Integration with the automation platform enables seamless communication between monitoring and control systems, providing operators with complete visibility of system performance while maintaining optimal chemical equilibrium conditions for maximum membrane longevity.
Prevent Membrane Degradation
Membrane integrity preservation requires understanding and controlling multiple degradation mechanisms that can impact reverse osmosis system performance. The primary factors affecting membrane longevity include chemical oxidation, hydrolysis, compaction, and physical damage from operational stress.
Chemical Degradation Prevention
- Maintain feed water pH between 2-11 for continuous operation
- Eliminate free chlorine exposure (maximum 0 ppm)
- Control feed water temperature below 85°F (29°C)
- Monitor SDI levels below 3.0
Degradation Type | Prevention Protocol | Monitoring Frequency |
---|---|---|
Chemical Oxidation | Dechlorination | Continuous |
Physical Damage | Pressure Control | Daily |
Biological Fouling | Sanitization | Monthly |
Mineral Scaling | Antiscalant Dosing | Continuous |
AXEON's HF5-Series Ultra Low Energy Membranes incorporate advanced thin-film composite technology that provides enhanced resistance to degradation while maintaining optimal performance characteristics. The pstrongoprietary membrane chemistry ensures:
- 5% nominal salt rejection
- 20% greater membrane surface area
- Superior chemical resistance
- Extended operational lifespan
Performance Optimization Strategies
- Implement automated pressure monitoring
- Maintain proper cross-flow velocity
- Execute regular cleaning cycles
- Monitor differential pressure trends
- Verify permeate quality daily
Degradation prevention protocols must include systematic maintenance procedures:
- Weekly performance data logging
- Monthly membrane cleaning assessment
- Quarterly comprehensive system evaluation
- Annual membrane replacement evaluation
Through proper implementation of these preservation strategies and regular monitoring of operational parameters, membrane degradation can be significantly reduced while maintaining optimal system performance. This proactive approach to membrane protection forms the foundation for implementing comprehensive long-term system protection measures.
The integration of AXEON's advanced membrane technology with proper maintenance protocols ensures maximum system efficiency and extended membrane life, leading to reduced operational costs and improved return on investment.
Implement Long-term System Protection
Long-term system protection requires a comprehensive approach that integrates preventive maintenance protocols with continuous performance monitoring to ensure optimal RO system operation. System longevity optimization depends on implementing structured maintenance schedules and adhering to established protection guidelines.
Maintenance Schedule Requirements
Maintenance Task | Frequency | Key Parameters |
---|---|---|
System Inspection | Daily | Pressure, Flow, TDS |
Chemical Cleaning | Monthly | pH, Conductivity |
Membrane Analysis | Quarterly | Rejection Rate, Flux |
Complete Service | Annual | All Components |
- Daily monitoring of operational parameters
- Weekly calibration of monitoring instruments
- Monthly chemical treatment assessment
- Quarterly performance evaluation
- Annual system optimization
AXEON's integrated protection strategy includes:
- Real-time performance monitoring systems
- Automated chemical dosing controls
- Predictive maintenance algorithms
- Remote system diagnostics
- Comprehensive operator training
System optimization requires maintaining:
- Proper cross-flow velocities
- Optimal recovery rates
- Balanced pH levels
- Controlled scaling indices
- Effective pretreatment
Long-term protection strategies must incorporate:
- Regular membrane cleaning cycles
- Systematic component replacement
- Continuous water quality monitoring
- Periodic system audits
- Updated operator certification
Through the implementation of these comprehensive maintenance protocols and protection measures, RO systems can achieve maximum operational efficiency and extended service life. Regular consultation with AXEON's technical support team ensures optimal system performance and reliability through every stage of operation.
This systematic approach to system protection, combined with proper operator training and regular maintenance, provides the foundation for sustained high-performance operation and maximum return on investment.
Conclusion
The comprehensive management of pH and bicarbonate levels in RO system design represents a critical foundation for achieving optimal system performance and longevity. Through precise control of chemical parameters, implementation of advanced monitoring systems, and strategic maintenance protocols, operators can maximize membrane life while minimizing operational costs. AXEON's integrated approach combines cutting-edge technology with over 35 years of water treatment expertise to deliver reliable, high-performance solutions that ensure consistent permeate quality and system efficiency.
By maintaining optimal pH ranges between 6.5-7.5, controlling bicarbonate scaling potential, and implementing proper antiscalant dosing strategies, facilities can achieve superior system performance while protecting their membrane investment. The synergy between precise chemical control and comprehensive monitoring systems enables proactive maintenance, preventing costly system failures and extending equipment life. This holistic approach to RO system management, supported by AXEON's advanced technology and technical expertise, provides operators with the tools needed to maintain peak efficiency while ensuring reliable, high-quality water production for years to come.
THE RIGHT SOLUTION FOR YOU
Contact us today for more information about our products and services.
CONTACT US