Technical Articles
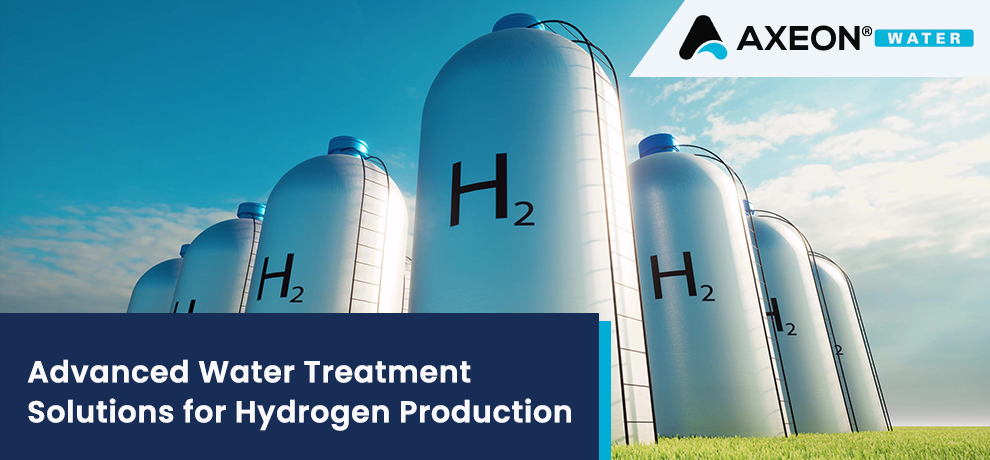
The hydrogen economy stands at a pivotal moment of transformation, with global markets projected to reach unprecedented levels by 2030. This revolution is fundamentally reshaping industrial processes, energy systems, and environmental sustainability initiatives. At the heart of this transformation lies the critical relationship between water quality and hydrogen production efficiency.
hydrogen producers face increasing demands for both quantity and quality. The industry requires ultra-pure water as a fundamental feedstock, with water quality directly impacting production efficiency, system longevity, and operational costs. This critical intersection of water treatment and hydrogen production has created a sophisticated market where advanced filtration technologies play a pivotal role.
Water Quality Challenges
The technical specifications for water used in hydrogen production represent some of the most stringent requirements in industrial processes. Water quality parameters must meet exacting standards to ensure optimal electrolyzer performance and prevent system degradation. The primary conductivity standard for electrolyzer feed water must maintain levels below 5 µS/cm, a requirement that demands sophisticated water treatment solutions.Impurity thresholds in hydrogen production water systems are precisely defined:
- Total Dissolved Solids (TDS) must not exceed 1.0 parts per million
- Silica concentrations must remain below 0.1 ppm
- Total Organic Carbon (TOC) levels must stay under 0.1 ppm
- Particle content must maintain turbidity below 1.0 NTU
The implications of poor water quality manifest in multiple ways throughout the hydrogen production process. Substandard water quality leads to electrode fouling, membrane degradation, and catalyst poisoning. These issues can reduce system efficiency by up to 40% and increase energy consumption by 25-30%. Furthermore, inadequate water treatment can reduce membrane lifespan by half and significantly increase maintenance frequency and associated costs.
AXEON's Advanced Solution Portfolio
AXEON's comprehensive water treatment solutions incorporate multiple technologies specifically engineered for hydrogen production applications. Our membrane filtration solutions represent the cornerstone of ultra-pure water production, featuring advanced reverse osmosis systems capable of achieving 99.5% salt rejection rates.The ultrapure water systems for electrolyzer feed incorporate multiple stages of treatment:
- Primary filtration utilizing advanced media filters
- High-recovery reverse osmosis systems
- Final polishing stages with electro deionization
- Continuous monitoring and control systems
Our reverse osmosis systems are engineered for various water sources:
- Tap water systems processing up to 50,000 gallons per day
- Brackish water systems handling up to 100,000 GPD
- Seawater desalination units capable of 200,000 GPD
Supporting Technologies AXEON's integrated approach combines multiple treatment technologies:
- Media filtration systems for pre-treatment
- Ion exchange systems for hardness removal
- UV sterilization for biological control
- Chemical injection systems for optimal performance
- Membrane cleaning systems for maintenance
Engineered Solutions for Specific Applications
Green hydrogen production requires specialized water treatment configurations optimized for electrolysis processes. These systems incorporate real-time monitoring and automated quality control measures to maintain consistent water quality parameters. The integration of smart technology enables predictive maintenance and performance optimization.Industrial applications benefit from custom-engineered solutions designed for specific processes:
- Steam methane reforming requires precise control of silica and hardness levels
- Coal gasification processes demand robust pretreatment systems
- Process water recycling incorporates advanced recovery technologies
The AXEON Advantage: Engineering Excellence
AXEON's 35-year legacy in membrane filtration technology translates into unparalleled expertise in system design and optimization. Our engineering capabilities extend beyond standard solutions to include custom-designed systems that address specific site requirements and operational parameters.Manufacturing excellence is assured through our USA-based production facilities, where ISO:9001 certification and Six Sigma processes ensure consistent quality. Our technical support team provides comprehensive consultation services, from initial system design through ongoing operational support.
The ROI optimization approach incorporates:
- Energy efficiency analysis and optimization
- Water recovery maximization strategies
- Maintenance requirement reduction
- System longevity enhancement
- Operational cost minimization
This comprehensive approach to water treatment system design and implementation ensures optimal performance in hydrogen production applications while minimizing operational costs and environmental impact.
Implementation and Support
AXEON's comprehensive implementation strategy begins with detailed system design and consultation. Our expert engineers work closely with clients to develop customized water treatment solutions that align perfectly with their hydrogen production requirements. The design phase incorporates advanced 3D modeling and simulation tools to optimize system layout and performance before installation begins.The installation guidance program encompasses detailed documentation, on-site supervision, and comprehensive training for operational staff. Our installation experts provide hands-on support throughout the commissioning process, ensuring every component is properly integrated and calibrated for optimal performance.
Operational support extends far beyond the initial setup. AXEON's dedicated technical team provides 24/7 assistance through multiple channels, including remote monitoring capabilities that allow real-time system optimization and troubleshooting. This proactive approach helps prevent potential issues before they impact production.
Our maintenance programs are structured around predictive and preventive strategies. Regular system health checks, performance audits, and scheduled maintenance activities are carefully documented and tracked. The maintenance schedule is customized based on specific operational parameters, water quality conditions, and production demands.
Performance monitoring utilizes advanced analytics and reporting tools that track key metrics including:
- Water quality parameters in real-time
- System efficiency and recovery rates
- Energy consumption patterns
- Component performance metrics
- Maintenance requirements and scheduling
Quality Assurance and Certification
AXEON's commitment to quality is demonstrated through rigorous adherence to ISO:9001 standards, ensuring consistent product quality and customer satisfaction. Our quality management system encompasses every aspect of operations, from design and manufacturing to installation and support.Six Sigma process controls are implemented throughout our manufacturing facilities, maintaining strict statistical control over all production processes. This approach has resulted in a defect rate of less than 3.4 parts per million, ensuring exceptional reliability in our water treatment systems.
Quality testing procedures involve multiple stages of verification:
- Component-level testing of all critical elements
- System-wide performance validation
- Extended run testing under simulated conditions
- Water quality analysis at multiple stages
- Pressure and flow rate verification
- Safety system validation
Our performance guarantees are backed by comprehensive documentation and warranty coverage, providing customers with complete confidence in their investment.
Cost-Benefit Analysis
Investment in AXEON's advanced water treatment systems delivers substantial financial benefits through multiple channels. Operational cost reduction is achieved through optimized energy consumption, reduced chemical usage, and minimized maintenance requirements. Typical systems demonstrate 30-40% reduction in operational expenses compared to conventional solutions.Equipment lifespan extension is realized through superior design and materials, coupled with advanced monitoring and maintenance programs. Our systems regularly achieve operational lifespans 40-50% longer than industry averages, significantly reducing the total cost of ownership.
Production efficiency gains are documented through:
- Increased throughput capacity
- Reduced downtime
- Improved product quality
- Lower reject rates
- Enhanced process stability
Environmental Impact
AXEON's commitment to environmental sustainability is reflected in our system designs and operational practices. Water footprint reduction is achieved through advanced recovery systems that typically achieve 85-95% efficiency, significantly reducing waste and conserving valuable water resources.Our sustainable practices extend beyond water conservation to include:
- Energy-efficient component selection
- Waste minimization strategies
- Chemical usage optimization
- Sustainable packaging initiatives
- Recycling programs for spent components
Our specialized solutions for hydrogen production demonstrate our support for green energy initiatives, contributing to the global transition toward renewable energy sources and reduced carbon emissions.
THE RIGHT SOLUTION FOR YOU
Contact us today for more information about our products and services.
CONTACT US