Technical Articles
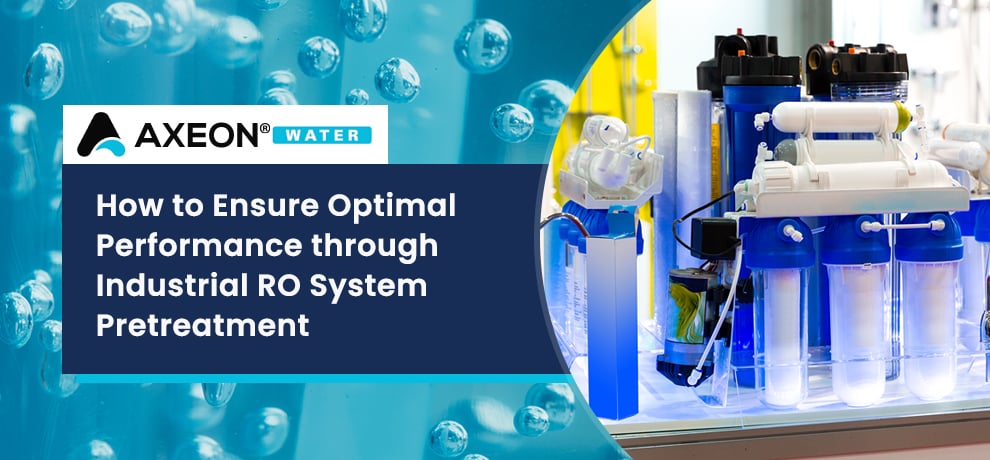
Pretreatment in industrial RO systems is essential for extending membrane life and improving system efficiency. Proper pretreatment protocols protect reverse osmosis membranes from fouling, scaling, and premature failure while ensuring consistent water quality and reduced operational costs. Through strategic implementation of multi-stage filtration, chemical dosing, and monitoring systems, industrial facilities can achieve optimal reverse osmosis performance and extended membrane longevity.
Understanding Reverse Osmosis Pre-treatment Fundamentals
Reverse osmosis pretreatment systems consist of multi-stage filtration and chemical treatment components that protect membrane elements from fouling and damage. The pretreatment process removes suspended solids, controls scaling potential, and eliminates harmful contaminants before water contacts the RO membranes.
Core Components of Pretreatment Systems
Multi-media filtration systems trap suspended particles and reduce turbidity to prevent membrane surface fouling. Granular media filters containing layers of anthracite, sand and garnet provide effective particle removal down to 10–15 microns. Cartridge filters act as a final barrier, capturing particles as small as 5 microns before water reaches the membranes.Critical Role in Membrane Protection
Proper pretreatment prevents premature membrane failure by controlling biological growth, scale formation, and organic fouling. Chemical dosing systems inject antiscalants to prevent calcium carbonate precipitation and scale deposits on membrane surfaces. Regular monitoring of the Silt Density Index (SDI) ensures optimal pretreatment performance and membrane protection.
Impact on System Longevity
Implementing effective pretreatment methods considerably prolongs the lifespan of membranes while ensuring consistent system performance. Effective pretreatment can significantly increase membrane lifespan by preventing fouling and physical damage. This reduces operational costs through fewer membrane replacements and cleaning cycles while ensuring reliable water production capacity.
Essential Components of Pretreatment Systems for Reverse Osmosis
Effective pretreatment systems incorporate multiple filtration and chemical treatment stages to protect reverse osmosis membranes and optimize system performance. Multi-media filtration systems utilize layers of anthracite, sand, and garnet to remove suspended solids down to 10-15 microns, preventing membrane surface fouling and maintaining stable SDI values.
Carbon Filtration Units
Granular activated carbon filters eliminate free chlorine and organic compounds that can damage membrane surfaces. These carbon filtration units reduce organic fouling potential while protecting the semipermeable membrane from oxidation damage. The carbon filters also improve water quality by removing taste, odor, and color-causing compounds.
Anti-scalant Dosing Systems
Chemical dosing systems inject precise amounts of antiscalant chemicals to prevent calcium carbonate precipitation and scale formation. These systems control scaling potential by preventing calcium sulfate, calcium phosphate, and other mineral deposits from forming on membrane surfaces during the reverse osmosis process.
Final Barrier Protection
Cartridge filter housings equipped with 5-micron security filters provide critical final barrier protection before water contacts the RO membranes. This last filtration stage captures any remaining particulates that could cause membrane fouling or damage. Regular monitoring of differential pressure across these filters ensures optimal pretreatment performance.
Optimizing Industrial Reverse Osmosis System Maintenance
Regular monitoring and preventive maintenance are critical for maintaining optimal RO system performance. Daily inspections of operating parameters, tracking performance data, and scheduled cleaning are essential to prevent membrane fouling and scaling.
Regular Monitoring Protocols
Continuous monitoring of key performance indicators like flow rates, pressure differentials, and conductivity levels ensures early detection of potential issues. The Silt Density Index (SDI) must be measured regularly to verify pretreatment effectiveness and prevent membrane surface fouling. Remote monitoring capabilities enable real-time tracking of system parameters and immediate response to deviations.
Performance Optimization Strategies
Strategic chemical dosing with antiscalants prevents calcium carbonate precipitation and scale formation on membrane surfaces. Operating pressure and recovery rates require regular adjustment based on feed water quality analysis. Proper flow distribution across membrane elements maintains consistent permeate production while minimizing concentration polarization.Preventive Maintenance Requirements
Scheduled maintenance includes inspection of membrane elements, cleaning of cartridge filter housings, and calibration of monitoring instruments. High-pressure pumps require regular servicing to maintain proper operating pressure and flow rates. Membrane autopsy and performance testing help identify early signs of fouling or damage.
Chemical Cleaning Procedures
Membrane cleaning protocols utilize specialized cleaning solutions to remove organic fouling, mineral scale, and biological growth. Clean-in-place (CIP) systems allow for periodic deep cleaning without membrane removal. The cleaning frequency depends on feed water quality and system operating conditions, typically requiring 6-8 hour CIP events at scheduled intervals.
Critical Parameters for Reverse Osmosis Systems Pretreatment
Feed water quality directly impacts membrane performance and system longevity. Raw water must meet stringent requirements including turbidity less than 1 NTU and SDI values below 3 to prevent premature membrane fouling. Regular monitoring of chloride ions, calcium carbonate scaling potential, and organic compounds ensures optimal pretreatment effectiveness.
SDI Monitoring and Control
The Silt Density Index (SDI) serves as a critical indicator of pretreatment system performance. Multi-media filtration and cartridge filters must maintain SDI values below 3 to protect membrane surfaces from particulate fouling. Regular SDI testing enables early detection of pretreatment issues before membrane damage occurs.
Chemical Dosing Optimization
Precise antiscalant dosing prevents calcium carbonate precipitation and scale formation on membrane surfaces. Chemical feed systems require regular monitoring and adjustment based on feed water quality analysis. Sodium bisulfite injection removes residual chlorine while pH adjustment chemicals optimize membrane performance.
Operating Pressure Considerations
Feed water pressure must remain between 45-85 psi for proper pretreatment system operation. The high-pressure pump maintains consistent flow rates through multi-media filters and cartridge housings. Differential pressure monitoring across pretreatment components enables early detection of fouling or scaling issues.
Advanced Pretreatment Technologies for Industrial RO
Ultrafiltration integration
Ultrafiltration systems provide superior membrane protection by removing particles down to 0.01 microns, ensuring optimal SDI values and preventing biological fouling. These advanced membrane surface systems integrate seamlessly with existing multi-media filtration to enhance overall system performance.
Automated Monitoring Systems
Sophisticated control panels with remote monitoring capabilities enable real-time tracking of critical parameters including flow rates, pressure differentials, and conductivity levels. Advanced technologies incorporate automated chemical dosing systems that adjust antiscalant and pH levels based on feed water quality analysis.
Chemical Optimization Techniques
Precise antiscalant dosing prevents calcium carbonate scaling and mineral deposits through automated feed systems. Chemical optimization includes:
- Sulfuric acid injection for pH control
- Sodium bisulfite addition for chlorine removal
- Customized antiscalant programs based on water chemistry
Remote Monitoring Capabilities
Cloud-based monitoring platforms provide 24/7 system oversight with:
- Real-time performance data tracking
- Automated alerts for operational parameters
- Predictive maintenance scheduling
- Quick turnaround times for system adjustments
Integrating advanced technologies maintains consistent water quality and lowers operational costs by optimizing chemical use and reducing membrane cleaning frequency.
Maximizing System Performance Through Effective Pre-treatment
Proper pretreatment directly impacts reverse osmosis system performance by optimizing recovery rates up to 75% while extending membrane longevity. Strategic implementation of multi-stage filtration and chemical treatment protocols ensures consistent permeate production and reduced operational costs.
Recovery Rate Optimization
Advanced pretreatment systems incorporate automated monitoring and chemical dosing to maintain optimal recovery rates between 65-75%. Multi-media filtration combined with antiscalant dosing prevents membrane fouling while maximizing permeate flow rates and minimizing concentrate waste.
Membrane Life Extension
Effective pretreatment extends membrane life by preventing calcium carbonate scaling, organic fouling, and biological growth. Regular monitoring of SDI values below 3 and proper chemical dosing reduces membrane cleaning frequency and replacement costs. Strategic implementation of cartridge filtration provides critical final barrier protection.
Operational Cost Reduction
Optimized pretreatment reduces operational costs through:
- Decreased membrane replacement frequency
- Lower chemical cleaning requirements
- Minimized downtime for maintenance
- Reduced energy consumption through maintained membrane performance
System Efficiency Improvement
Proper pretreatment maintains consistent system performance by preventing membrane surface fouling and scaling. Automated monitoring systems with remote capabilities enable real-time optimization of operating parameters including pressure, flow rates, and chemical dosing to ensure reliable water production capacity.
To Sum Up
Implementing comprehensive pretreatment protocols is essential for ensuring optimal industrial RO system performance and longevity. Through strategic multi-stage filtration, chemical dosing optimization, and automated monitoring systems, facilities can prevent membrane fouling while maintaining consistent water quality. AXEON Water Technologies delivers advanced pretreatment solutions that protect membrane elements, reduce operational costs, and maximize system efficiency across diverse industrial applications. Regular maintenance combined with proper pretreatment protocols ensures reliable operation and extended membrane life.
THE RIGHT SOLUTION FOR YOU
Contact us today for more information about our products and services.
CONTACT US