Technical Articles
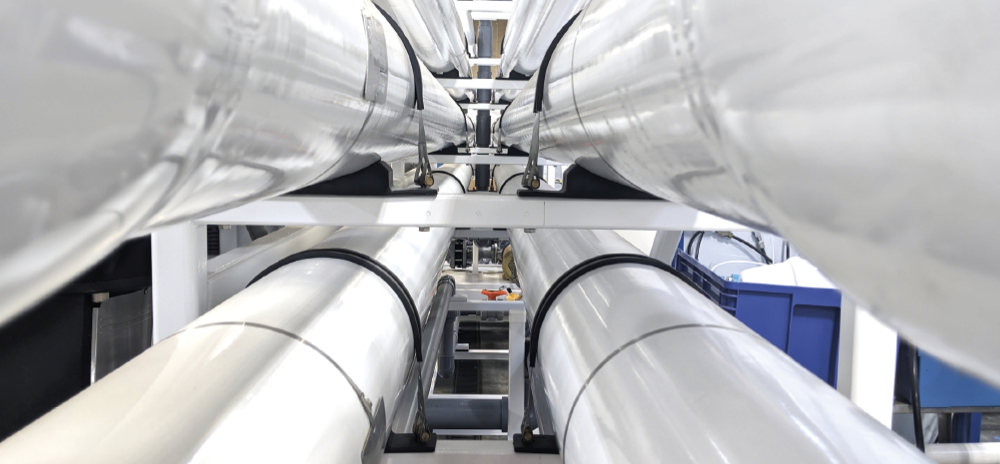
WINTERIZING A REVERSE OSMOSIS SYSTEM: LONG-TERM RO SYSTEM SHUTDOWN AND PRESERVATION
A reverse osmosis (RO) system or nanofiltration (NF) system, as part of a water treatment solution is typically exposed to varying operating conditions. However, changes in operating conditions may warrant the need for long term system shut down or relocation of the system. Such deviations in a normal operating schedule require special care and precaution to ensure proper future performance and functioning of the membrane system and its key components. Generally, the biggest threats to a membrane system that is currently static or on a reduced operating schedule are freezing and microbiological growth. To address these threats, this article will discuss the appropriate steps of shutting down, preserving, and storing a system to ensure that future functionality remains optimal.
The shutdown operation of a RO or NF system is the first and one of the most important steps in ensuring proper subsequent preservation and storage. Typically, RO and NF systems are designed to handle continuous operation, which reduces the likelihood of significant product TDS variation, as well as providing a limited environment for microbiological growth. As soon as continuous or near-continuous operation is disrupted, microbes are given nearly free reign to reproduce and form biofilms on both the feed and concentrate plumbing of the system, including the membranes. This condition is termed biofouling. If left unchecked, biofouling may result in permeate flow loss and the need to increase feed pressure to achieve the same production rate. More importantly, the effects manifested by biofouling may give rise to decreased membrane system efficiency and higher energy costs. In order to reduce this risk factor, several key steps should be performed during system shut down.
During the shutdown of a membrane system, the membranes should first be flushed with permeate water. However, in cases where a large quantity of permeate water is not available, high quality (treated) feed water may be used as an appropriate substitute. Typically, what is meant by high quality feed water is softened dechlorinated municipal or well water with an SDI <3. The purpose of flushing the membranes with pure or relatively pure water is to remove any water present in the system that contains a high concentration of impurities; this is especially important on systems that have multiple membranes in series, where the membranes in the final stage may experience elevated concentrations of impurities. Most importantly, flushing with high purity water will ensure that the concentrate conductivity matches closely to the conductivity of the permeate produced by the membrane system.
When flushing the membrane system during the shutdown procedure, a pressure of around 40 psi will suffice in most applications. Iit is also worth noting that this procedure should not be done at a high pressure. During normal or continuous operation, a high feed flush flow rate may offer an added beneficial cleaning effect, but it is important to keep in mind that if multi-element vessels are used, then close attention should be paid in ensuring that membrane pressure drops do not exceed the specifications stated by the manufacturer. Another consideration when flushing a membrane system during shut down is that the water used for flushing should never contain pretreatment chemicals. Phosphate-based scale inhibitors are especially discouraged as they promote organic growth. In addition, all chemical injection systems should be stopped prior to membrane flushing.
In conjunction with flushing, there are several plumbing considerations of the membrane system that need to be taken into consideration, to ensure the most effective flush possible. If the concentrate line ends in a drain below the level of the pressure vessels, a siphoning effect may empty even the most carefully flushed system; this is especially true for systems containing horizontal pressure vessels. To combat this effect, an air break should be utilized in the concentrate line at a position higher than the highest-pressure vessel. Another plumbing consideration is that if the permeate line is pressurized during operation and the system faces unexpected shutdowns, the membranes may become exposed to a deleterious static permeate backpressure, which can delaminate the membrane flat sheet contained within each membrane element. If this backpressure exceeds 5 psi, it may result in irreversible damage to the membranes; hence, check valves or atmospheric drain valves may be used to safeguard the membranes.
One final note on membrane system shutdown is that special precautions should be taken if a system is shut down for a period greater than two days. Special care should be taken to ensure that the membrane elements do not dry out. When a membrane dries out, it will permanently lose flux and performance will suffer tremendously. There are techniques to help restore flux in dried elements, such as using an isopropyl alcohol/propylene glycol mix to help open permeate channels in the desiccated flatsheet; however, this is mostly a stop gap measure and should not be performed unless absolutely necessary. In addition, extended shut down necessitates that the system is protected from biological growth and temperature extremes; the next section will deal with this topic exclusively.
After flushing of the reverse osmosis or nanofiltration system, preservation should follow within the next ten hours. Optimally, the system should be pumped full of either a 1.0-1.5% solution of AXEON M-100. Preservative should be introduced into the system using what is called the overflow technique, where the M-100 preservative is circulated in such a way that all remaining air in the system is minimized after the recirculation is completed. After all the pressure vessels have been filled, preservative solution should be allowed to overflow through an opening located higher than the uppermost pressure vessel. In the case of using M-100, the preservation solution must be isolated from outside air by closing all valves on the membrane system; any contact with oxygen will oxidize the M-100. In addition, a M-100 preservative will require periodic checking of pH on a weekly basis; when the pH drops below 3, the preservation solution must be changed to ensure resistance to biological growth. Using proprietary alternative preservatives has its advantages in this case, as some of these preservatives are much more resistant to oxidation and pH shift.
In addition to preservation from biological growth, protection from freezing may be necessary in regions that experience sub-zero temperatures on a frequent basis. Water contained within a RO or NF system at freezing temperatures will start to expand as it freezes; this expansion force will damage the weakest points in the system. Some of the negative effects of a membrane system encountering freezing temperatures are:
- Damaged fittings and Pipings
- Damaged pump components
- Damaged housings
- Damaged membrane elements
In this case it may be necessary to supplement preservative solutions with a propylene glycol additive to lower the freezing point. By varying the propylene glycol concentration, resistance to freezing may be increased or decreased. For example, a 20% propylene glycol solution will lower the freezing point of the water inside a membrane system to approximately 20 degrees Fahrenheit. From a technical standpoint, the glycol acts to disturb formation of any ice crystal lattice and subsequent nucleation (state of change) of water molecules to ice. Adding a higher percentage of propylene glycol will allow even further resistance to freezing (see tablefig. 1 below).
Freezing Points of Propylene Glycol / Water Mixtures | |
Propylene Glycol Wt.% (Vol.%) | Freezing Point °F(°C) |
0 (0) | 32 (0) |
10 (10) | 25 (-4) |
20 (19) | 20 (-7) |
30 (29) | 10 (-12) |
40 (40) | -5 (-21) |
50 (50) | -30 (-34) |
60 (60) | -60 (-51) |
70 (70) | <-60 (<-51) |
80 (80) | <-60 (<-51) |
90 (90) | <-60 (<-51) |
100 (100) | <-60 (<-51) |
Below are some summarized guidelines when shutting down and preserving a RO or NF membrane system:
- Make sure any electrical connections are turned off and safely disconnected if the membrane system is to be moved or relocated.
- Flush the system with permeate or high-quality feed water.
- Make sure the plumbing configuration prohibits siphoning of water out of the pressure vessels and eliminates the chance of momentary permeate backpressure.
- Immediately after flushing, preserve the membrane system with a M-100 solution; if freezing temperatures are to be encountered, supplement the preservative solution with the proper percentage of propylene glycol to help prevent freezing.
Membrane systems are generally designed for continuous operation. However, when a system must be shut down for more than 4 days, proper flushing, preparation, and preservation is essential. Flushing will ensure the membrane elements are surrounded by a clean, homogenous source of water. Preservation will help safeguard membranes and any associated equipment from biological growth and freezing temperatures.
Prevent Your Reverse Osmosis System from Freezing and Biofouling
If you do not intend to use your AXEON reverse osmosis (RO) system for several months during the cold season, it is recommended that you take the following steps to safeguard your system against freezing and microbiological growth. Protecting your system from these factors will prolong the life of the plumbing, flow meters, membranes and housings.
The following procedure is being provided only as a guideline and is for general use. This procedure will require the preparation of a winterizing solution.
Preparation: Using a clean, appropriate size bucket, prepare a solution in the ratio of one (1) pound of M-100 Membrane Preservative to four (4) gallons of good quality water (preferably permeate water). See Table 1 for food-grade Propylene Glycol freezing point calculations. Caution: Do not use ethylene glycol (i.e. anti-freeze for automobiles).
Step 1: Refer to your owner’s manual for the flushing procedure.
Step 2: Disconnect the system from all electrical sources.
Step 3: Turn off the feed water source and disconnect the unit from the feed water source.
Step 4: Remove the prefilters from their housings and drain the housings.
Step 5: Disconnect the bottom tubing from the back of the flow meters and allow them to drain.
Step 6: Disconnect the bottom tubing from the membrane housing and allow housing to drain.
Step 7: Disconnect the permeate tubing from the storage tank and drain permeate storage tank into a clean bucket (use this permeate water for preparation of the winterizing solution described above).
Step 8: After the unit has drained, reinstall prefilter housings and reattach tubing to flow meters, membrane housing, and storage tank.
Step 9: Close concentrate valve and recycle valve (if applicable).
Step 10: Remove the end caps from the top of each membrane housing.
Step 11: Fill each membrane housing with the winterizing solution.
Step 12: Reinstall the end caps onto the top of the membrane housings.
The reverse osmosis system can be left in storage for up to six months.
Please see the table below for appropriate amount of water to mix with the M – 100 for AXEON systems
500 | 0.5 Gallon |
1,000 | 0.75 Gallon |
1,500 | 1 Gallon |
2,000 | 1.5 Gallon |
4,000 | 3 Gallons |
5,000 | 3.5 Gallons |
7,000 | 5 Gallons |
9,000 | 6 Gallons |
10,000 | 7 Gallons |
How to properly restart your RO system following winterization
Step 1: Keep the permeate water line to drain for this procedure.
Step 2: Fully open the concentrate valve (counter clockwise).
Step 3: Fully close the recycle valve (clockwise)(if applicable).
Step 4: Plug in the RO system. Turn the system on and adjust the concentrate (waste) valve, recycle valve (if applicable), and the bypass screw on the pump to the designed flow and pressure.
Step 5: Turn the feed water on via the feed solenoid valve bypass or switch and let the system purge until no visible bubbles appear from the concentrate flow meter.
Step 6: Inspect the system for leaks.
Step 7: Allow the system to run for one hour to flush the preservative solution from the system.
Step 8: After one hour, shut down the system.
Step 9: Re-direct the permeate water back to the tank and then turn the system back on.
Step 10: Record the readings daily for a week. After a week, record the readings once a week.
DISCLAIMER: This information serves as a general guideline; when operating and storing a membrane system, always consult a water treatment professional or application engineer for best practices.
THE RIGHT SOLUTION FOR YOU
Contact us today for more information about our products and services.
CONTACT US